- Spawalnictwo
- 0 polubienia
- 20385 odsłony
- 0 komentarze
- tablica narzędziowa, urządzanie garażu, garaż, uchwyty na narzędzia, projekt warsztatu
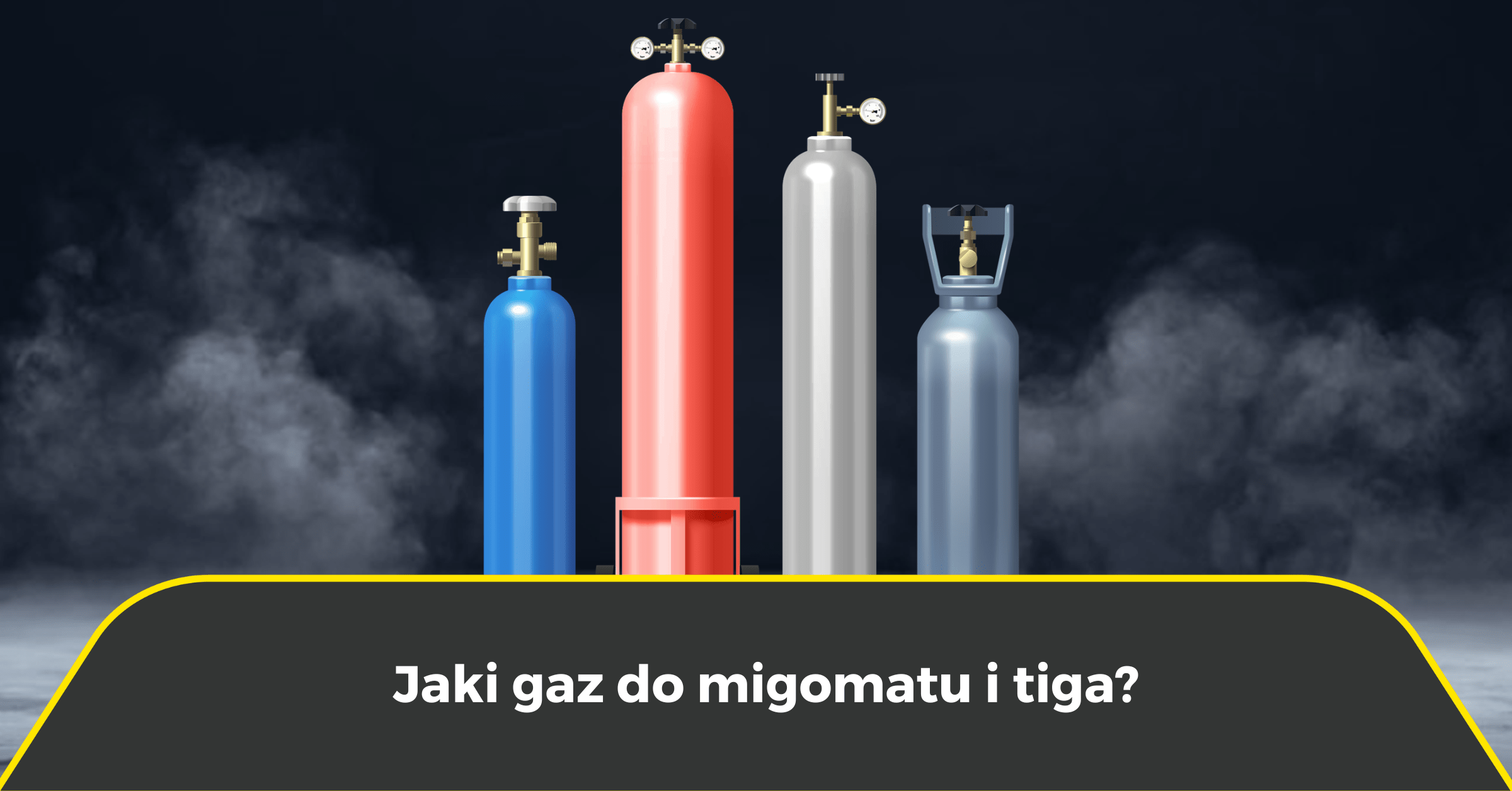
Procesy spawalnicze takie jak TIG, MIG i MAG wymagają zastosowania gazów lub specyficznych mieszanek gazów, które odgrywają kluczową rolę w zachowaniu właściwości materiału i jakości finalnego połączenia. Gazy te tworzą osłonę, która chroni topiony i podgrzewany materiał przed oddziaływaniem powietrza zewnętrznego.
Dodatkowo, gazy te tworzą korzystne środowisko dla powstawania i utrzymania łuku elektrycznego, który jest nieodzownym elementem procesu spawania. Jeśli podczas procesu spawania powietrze zewnętrzne zyska dostęp do metalu, obecny w nim tlen może prowadzić do utlenienia, a azot do nadmiernej porowatości lub kruchości materiału.
Z uwagi na często pojawiające się pytania na temat wyboru odpowiedniego gazu do spawania, zdecydowaliśmy się stworzyć ten artykuł. Odkryj, jakie gazy osłonowe są najczęściej stosowane w spawalnictwie i w których technikach spawalniczych są one najbardziej przydatne.
Typy gazów - czym są gazy aktywne i obojętne?
Gazy obojętne - zwane również gazami szlachetnymi lub inertnymi, są grupą pierwiastków chemicznych, które cechują się niską reaktywnością chemiczną. Obejmują one hel (He), neon (Ne), argon (Ar), krypton (Kr), ksenon (Xe) i radon (Rn). Dzięki swojej obojętności chemicznej, gazy te nie wchodzą w reakcje z większością substancji, w tym z metalami podczas spawania. W spawalnictwie gazy obojętne, takie jak argon i hel, są często wykorzystywane jako gazy osłonowe, chroniąc spawane metale przed reakcjami z innymi gazami.
Gazy aktywne - w kontekście spawania, to gazy, które mogą wchodzić w reakcje chemiczne z metalem podczas procesu spawania. Najczęstszym przykładem gazu aktywnego stosowanego w spawalnictwie jest dwutlenek węgla (CO2). Wysoka temperatura procesu spawania powoduje rozpad CO2 na składniki, w tym na tlen, który może reagować z metalem. To może prowadzić do utlenienia i innych zmian w strukturze spoiny. Inne gazy aktywne to tlen (O) i mieszaniny zawierające tlen lub dwutlenek węgla, które są często używane w procesach spawania MAG.
Wybór pomiędzy gazem obojętnym a aktywnym zależy od wielu czynników, takich jak rodzaj spawanego metalu, technika spawania, czy pożądane cechy spoiny. Obydwa rodzaje gazów mają swoje zastosowania w spawalnictwie i mogą znacząco wpływać na wynik końcowy procesu spawania.
Rodzaje gazów osłonowych i ich zastosowanie
Argon (Ar) - Jest najczęściej wykorzystywanym gazem osłonowym w spawalnictwie. Stosowany jest głównie w metodach TIG i MIG, szczególnie do spawania metali nieżelaznych, jak aluminium czy tytan, jak również stali nierdzewnej.
Hel (He) - Jest nieco droższy od argonu, ale zapewnia wyższe prędkości spawania i lepsze przenikanie ciepła. Zwykle stosowany w spawaniu TIG metali nieżelaznych.
Dwutlenek węgla (CO2) - Jest to najtańszy gaz osłonowy, najczęściej stosowany w spawaniu MAG. Dwutlenek węgla daje twardszy i bardziej niestabilny łuk spawania, w porównaniu do argonu, co może skutkować większą ilością rozprysków i porowatością spoiny.
Mieszanka argonu i dwutlenku węgla (Ar/CO2) - Ta kombinacja gazu jest często stosowana w spawaniu MAG, zwłaszcza stali węglowych i niskostopowych. Zwykle, argon stanowi większość mieszanki, z dodatkiem CO2 do stabilizacji łuku.
Mieszanka argonu, helu i dwutlenku węgla (Ar/He/CO2) - Gaz osłonowy do spawania metodą MAG stali austenitycznych, ferrytycznych i duplex łukiem zwarciowym, natryskowym i pulsującym, ręcznie lub w sposób zmechanizowany. Zalecany przy grubych elementach. Poprawia wtopienie i wygląd lica spoiny, daje niewielką ilość odprysków.
Mieszanka argonu i helu (Ar/He) - Ta mieszanka gazu jest używana w procesie spawania TIG do osiągnięcia większej prędkości spawania i głębszego przenikania ciepła.
Czystość gazów spawalniczych
Czystość gazu, w tym argonu, jest istotnym czynnikiem do rozważenia podczas spawania, zwłaszcza podczas spawania metodą TIG i MIG, gdzie argon jest często wykorzystywany jako gaz osłonowy. Czystość gazu odnosi się do procentowej zawartości konkretnego gazu w mieszaninie.
Oznaczenia 4.0, 4.5 oraz 5.0 odnoszą się do czystości gazu wykorzystywanego w różnych procesach, w tym w spawaniu.
Klasa 4.0: oznacza gaz o czystości 99,99%. To jest standardowy poziom czystości stosowany w wielu zastosowaniach przemysłowych.
Klasa 4.5: oznacza gaz o czystości 99,995%. Tak wysoka czystość jest często wymagana w specjalistycznych procesach, takich jak spawanie precyzyjne lub spawanie metali szlachetnych.
Klasa 5.0: oznacza gaz o czystości 99,999%. To jest najwyższy standard czystości gazu i jest zazwyczaj stosowany w bardzo specyficznych zastosowaniach, takich jak badania naukowe, elektronika czy przemysł farmaceutyczny. Pamiętaj, że wyższa czystość gazu zazwyczaj wiąże się z wyższymi kosztami, dlatego zawsze warto dokładnie rozważyć, jaka czystość jest rzeczywiście potrzebna do konkretnego procesu.
Na przykład, argon o czystości 99,995% oznacza, że tylko 0,005% mieszaniny stanowią inne gazy.
Wybór odpowiedniej czystości argonu zależy od kilku czynników, w tym od rodzaju metalu, który jest spawany, od techniki spawania oraz od wymagań dotyczących jakości końcowego produktu.
Spawanie TIG: W spawaniu TIG, które jest często wykorzystywane do spawania metali takich jak stal nierdzewna, aluminium czy tytan, zaleca się użycie argonu o wysokiej czystości, często na poziomie 99,995% lub wyższym. Dzięki temu uzyskuje się stabilniejszy łuk, lepszą ochronę przed oksydacją i lepszą jakość spoiny.
Spawanie MIG: W spawaniu MIG, zwłaszcza przy spawaniu stali węglowych i niskostopowych, czystość argonu może być nieco niższa, choć nadal zalecane jest stosowanie argonu o czystości co najmniej 99,95%. Argon w spawaniu MIG jest często mieszany z innymi gazami, takimi jak CO2 lub O2, co wpływa na ogólną czystość mieszanki. Wszystko zależy od specyfiki zastosowania - w niektórych przypadkach, np. przy spawaniu niektórych metali szlachetnych lub w specyficznych branżach, takich jak lotnictwo czy medycyna, mogą być wymagane wyższe standardy czystości gazu. Jednak ważne jest, aby pamiętać, że wyższa czystość gazu często wiąże się z wyższymi kosztami, dlatego ważne jest, aby zrównoważyć wymagania dotyczące jakości z ograniczeniami budżetowymi.
Wybór gazu w zależności od spawanego materiału
Jaki gaz do stali czarnej (stal węglowa i niskostopowa)?
- Dwutlenek węgla (CO2): CO2 jest ekonomicznym wyborem dla spawania MAG stali węglowej. Ułatwia głębokie wtopienie w materiał, jednak może prowadzić do większej ilości rozprysków i porowatości spoiny.
- Mieszanka argonu i dwutlenku węgla (Ar/CO2): Mieszanka ta zapewnia większą stabilność łuku i mniejszą ilość rozprysków w porównaniu do czystego CO2. Jest to najczęściej wybierana mieszanka gazów do spawania konstrukcji stalowych.
Jaki gaz do nierdzewki (stali nierdzewnej)?
- Argon (Ar): Argon jest często wykorzystywany do spawania TIG stali nierdzewnej ze względu na jego zdolność do utrzymania czystego i stabilnego łuku.
- Mieszanka argonu i dwutlenku węgla (Ar/CO2): Stosowana przy spawaniu MAG stali nierdzewnej.
- Mieszanka argonu i tlenku węgla (Ar/CO): Używana w spawaniu MIG/MAG, pomaga w utrzymaniu czystości stali nierdzewnej podczas procesu spawania.
Jaki gaz do aluminium i jego stopów?
- Argon (Ar): Ze względu na wysoką stabilność i jego niską reaktywność, argon jest najczęściej wybieranym gazem osłonowym do spawania aluminium. Zapewnia stabilny łuk spawalniczy i optymalną ochronę przed utlenianiem.
- Mieszanka argonu i helu (Ar/He): W niektórych przypadkach, zwłaszcza przy grubszych materiałach, ta mieszanka może zapewnić lepsze przenikanie ciepła i większą prędkość spawania.
Jaki gaz do metali nieżelaznych (np. miedź, tytan, nikiel)?
- Argon (Ar): Z powodu swojej inertności, argon jest dobrą opcją do spawania większości metali nieżelaznych.
- Hel (He): Zapewnia lepsze przenikanie ciepła i większą prędkość spawania w porównaniu do argonu, choć jest droższy.
Jaki gaz do stali wysokostopowych i materiałów trudno spawalnych?
- Mieszanka argonu, helu i dwutlenku węgla (Ar/He/CO2): Ta mieszanka jest stosowana do spawania metali trudno spawalnych lub o dużej grubości, umożliwiając uzyskanie głębszego przenikania ciepła i stabilnego łuku.
Jak ustawić przepływ gazu podczas spawania metodą MIG, MAG oraz TIG?
Dobór odpowiedniego przepływu gazu osłonowego jest kluczowy dla procesu spawania. Przepływ jest mierzony w litrach na minutę (l/min) lub stóp sześciennych na godzinę (cfh). Zbyt mały przepływ gazu może prowadzić do niewystarczającej ochrony spoiny, natomiast zbyt duży przepływ może prowadzić do niepotrzebnego marnowania gazu oraz powodować powietrza, które z kolei mogą wprowadzić zanieczyszczenia do strefy spawania.
Spawanie MIG/MAG: Dla większości zastosowań spawania MIG/MAG, przepływ gazu osłonowego powinien wynosić od 15 do 25 l/min. Wyższy przepływ może być konieczny w warunkach, gdzie występuje silny wiatr.
Ogólna zasada, która jest często stosowana w metodzie MIG/MAG polega na tym, że na każdy milimetr średnicy dyszy spawalniczej przypada 1 litr na minutę (l/min) przepływu gazu osłonowego. Na przykład, jeśli średnica dyszy spawalniczej wynosi 12 mm, zgodnie z tą zasadą, przepływ gazu osłonowego powinien wynosić 12 l/min. Jednakże, warto pamiętać, że jest to zasada ogólna i faktyczny optymalny przepływ gazu może zależeć od wielu czynników, takich jak rodzaj gazu osłonowego, materiał, który jest spawany, technika spawania oraz specyficzne warunki środowiskowe. Dlatego zawsze warto skonsultować się z instrukcjami producenta sprzętu spawalniczego lub z doświadczonym specjalistą ds. spawania.
Spawanie TIG: Ze względu na delikatność procesu spawania TIG, przepływ gazu osłonowego zwykle jest mniejszy w porównaniu do spawania MIG/MAG. Zazwyczaj przepływ argonu w spawaniu TIG wynosi od 5 do 15 l/min, w zależności od wielkości elektrody i mocy spawania.Jednym z najważniejszych czynników wpływających na wybór przepływu gazu jest wielkość dyszy spawalniczej - większe dysze wymagają większego przepływu gazu. Ponadto, warto zauważyć, że materiał, który jest spawany, rodzaj gazu osłonowego, a także specyficzne warunki środowiska (np. silny wiatr w miejscu spawania) mogą wymagać dostosowania przepływu gazu.
Rodzaje butli gazowych
Butle gazowe są dostępne w różnych rozmiarach i typach, które są dostosowane do konkretnych wymagań różnych aplikacji. Poniżej znajduje się opis różnych rodzajów butli gazowych:
Butle wysokociśnieniowe: Są one najczęściej stosowane do przechowywania gazów spawalniczych, takich jak argon, tlen, azot, acetylen czy hel. Te butle są zaprojektowane do utrzymania wysokiego ciśnienia wewnętrznego, często dochodzącego do 200 barów. Wykonane są zazwyczaj ze stali nierdzewnej lub stali wysokowęglowej, które są odporne na korozję i wytrzymałe na wysokie ciśnienia. Dostępne są w różnych rozmiarach, najczęściej od około 5 litrów do 50 litrów.
Wiązki butlowe: To zbiory kilkunastu butli, które są trwale połączone ze sobą, co pozwala na ciągłą pracę bez konieczności wymiany butli. Wiązki butlowe są szczególnie przydatne w przemyśle ciężkim lub w dużych zakładach produkcyjnych, gdzie wymagane jest ciągłe dostarczanie gazu.
Zbiorniki kriogeniczne: Te zbiorniki służą do przechowywania gazów w formie ciekłej, takich jak ciekły azot czy argon. Są to duże zbiorniki, które są często używane tam, gdzie potrzebna jest duża ilość gazu, jak na przykład w przemyśle metalurgicznym lub chemicznym. Dzięki temu, że gazy są przechowywane w formie ciekłej, zbiorniki kriogeniczne mogą przechowywać znacznie większe ilości gazu niż tradycyjne butle gazowe o porównywalnym rozmiarze.
Każdy typ butli ma swoje unikalne zastosowania i wybór odpowiedniego typu zależy od konkretnych wymagań użytkownika, takich jak ilość potrzebnego gazu, dostępność miejsca na przechowywanie oraz dostępność urządzeń do napełniania i obsługi.
Oznaczenia butli gazowych
Butle gazowe są zazwyczaj oznaczone różnymi kolorami i etykietami, które wskazują, jaki rodzaj gazu zawierają. Te oznaczenia są ważne dla bezpieczeństwa i są regulowane przez normy europejskie, takie jak EN-1089-3. Poniżej znajduje się więcej szczegółów na temat tych oznaczeń:
Oznaczenia kolorystyczne: Kolor butli gazowej jest jednym z najbardziej oczywistych oznaczeń, które wskazują na to, jaki gaz zawiera. Na przykład, butle zawierające acetylen są zazwyczaj oznaczone kolorem kasztanowym, butle z helem są oznaczone kolorem brązowo-szarym, mieszanki z wodorem są oznaczone kolorem czerwono-szarym, a butle z azotem są oznaczone kolorem czarno-szarym.
Etykiety i nalepki: Butle gazowe muszą zawierać etykiety i nalepki, które dostarczają szczegółowych informacji o zawartości butli. Te informacje mogą obejmować ostrzeżenia i zalecenia dotyczące bezpieczeństwa (zwroty R i S), zgodność z przepisami ADR dotyczącymi transportu, wzory chemiczne gazu lub mieszanin gazu, nazwę handlową produktu, pełne określenie gazu, numer EWG dla gazu jednoskładnikowego lub określenie "mieszanina gazowa", wskazówki producenta i dane kontaktowe producenta.
Numery EWG: Numery EWG (Europejskie Wspólnoty) są unikalnymi identyfikatorami używanymi do klasyfikacji substancji chemicznych. Dla gazów jednoskładnikowych, numer EWG powinien być wyraźnie zaznaczony na etykiecie butli.
Wskazówki producenta: Te informacje, które mogą zawierać instrukcje dotyczące prawidłowego przechowywania i użycia gazu, są również ważnym elementem oznaczeń butli gazowej.
Pamiętaj, że niezależnie od oznaczeń na butli gazowej, zawsze należy postępować zgodnie z instrukcjami producenta i przestrzegać odpowiednich zasad bezpieczeństwa podczas przechowywania i użytkowania butli gazowych.
Butla mieszanka argon/CO2 8 litrów /...
Zestaw butla MIX Ar/CO2 + reduktor...
Zestaw butla MIX Ar/CO2 + butla argon...
Zestaw butla argon (Ar) + reduktor z...
Spawarki MIG/MAG
Spawarka Ideal V-MIG 280 4x4 Digital...
Spawarka ESAB Origo MIG C340 PRO 4WD...
Spawarka Ideal Tecnomig 212 LCD...
Spawarka Ideal Tecnomig 200/2 MMA -...
Spawarka Weldman Micro MIG 200 - zestaw
Spawarka Magnum MIG 291 Alu/Cu...
Spawarka Ideal Praktik MIG 200 Pulse...
Spawarka Spartus EasyMIG 210S - zestaw
Spawarka GEKO MIG/TIG/MMA-220 - zestaw
Spawarka GEKO MIG/TIG/MMA-160 - zestaw
Spawarki TIG
Spawarka Ideal V-TIG 225 Puls
Spawarka ESAB Caddy TIG 2200i AC/DC...
Spawarka Ideal Expert TIG 300 DC...
Spawarka Spartus EasyTIG 208P AC/DC -...
Spawarka Spartus ProTIG 225P AC/DC -...
Spawarka ESAB Rogue ET 200iP PRO -...
Spawarka ESAB Rogue ET 180i DC - zestaw
Spawarka ESAB Caddy TIG 2200iw AC/DC...
Spawarka Welder Fantasy JET TIG 200...
Spawarka Welder Fantasy JET TIG II...
Inne kategorie w dziale spawalnictwo
- Spawalnictwo
- Spawarki MIG|MAG
- Spawarki TIG
- Spawarki MMA
- Przecinarki plazmowe
- Materiały spawalnicze
- Ochrona spawacza
- Uchwyty spawalnicze
- Uchwyty plazmowe
- Chemia spawalnicza
- Urządzenia do czyszczenia spoin i akcesoria
- Pozycjonery i obrotniki
- Sprzęt gazowy
- Części do urządzeń spawalniczych
- Akcesoria spawalnicze